Performing supply chain due diligence is a daunting task, especially for small and medium-scale enterprises (SMEs) that often face capacity challenges. Sourcing traceable materials and building transparent supply chains requires time, financial investment, whole company buy-in, and conversations with suppliers that can be tough.
In the Human Rights Watch report ‘The Hidden Cost of Jewelry’, eight criteria for responsible sourcing were laid out (remind yourself of those here). We believe that, while welcome, the criteria are aspirational at best. With so many competing priorities holding their attention, many jewellery industry professionals will find it difficult to get started on meeting the criteria.
There are lots of capacity barriers for businesses large and small, and, contrary to public perception, many are unrelated to wilful complacency. From our work in the jewellery industry, we have identified three capacity barriers to effective supply chain due diligence: human resources, knowledge gaps, and company and supplier willingness.
Human Resources
Employees of smaller companies tend to have diverse responsibilities and therefore competing priorities. In business, effective prioritisation is key to success, so it’s unsurprising (and understandable) that many smaller businesses prioritise immediate sales, marketing, bookkeeping and HR above responsible sourcing considerations.
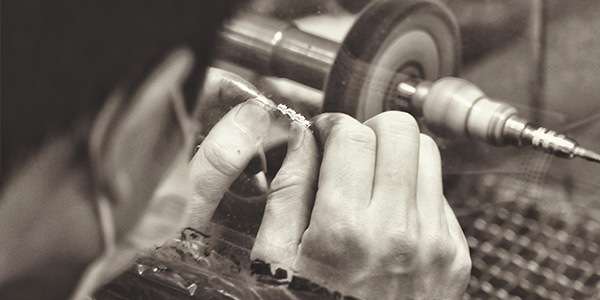
Environmental and human rights supply chain due diligence is required by both hard and soft laws and yet the business case may not be immediately obvious to individual employees or their bosses. For that reason, many companies focus only on compliance with mandatory rules (e.g. national law) or commercially essential rules (e.g. of guilds, bourses, industry associations, etc.). Until the financial, reputational, legal and performance benefits of well-managed supply chains that incorporate traceable materials is clear, it may be difficult to justify allocating staff time to learning about proper due diligence systems, and operationalising them within the company. Establishing the business case for due diligence and communicating it to company leadership is thus vital if human resources are to be diverted to do responsible sourcing.
Knowledge Gaps
Companies sometimes lack knowledge of what it means to perform due diligence on social and environmental risks in supply chains. While there are a number of training programmes available on technical supply chain due diligence, these are often not context-specific and so may not cover the particular issues jewellery companies or their suppliers may face.
Although some companies may be aware of the potential presence of certain risks in their supply chains, a lack of knowledge on proper, proactive risk management processes may make the performance of due diligence appear more daunting than it really is. Ultimately, many companies fear the unknown: if I invest in the performance of due diligence on my supply chain and discover it contributes to human rights abuses, what do I do? Am I responsible for remedying the risk? What will that process be like? How much will it cost me? Furthermore, will I lose business and my relationship with my supplier? Keeping supply chains in the dark can be seen as a way to avoid risk – what you don’t know can’t hurt you, right? And yet time and again we meet companies who did just that and down the line were presented with allegations from civil society and a big mess to clear up.
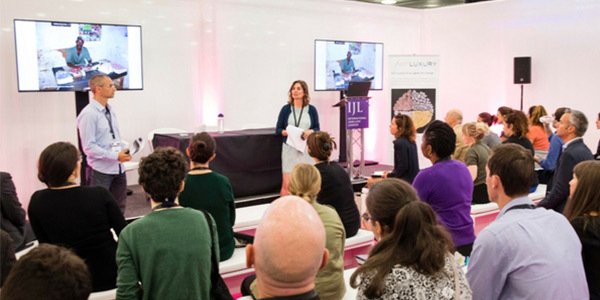
Companies need to understand that social and environmental risks, like any other business risk, can be managed through risk control processes, including preventative, detective, and corrective measures. However, to put in place such controls, personnel must first understand the risks in the supply chain. Knowledge is power. In order to obtain that knowledge, the team (and senior management) must be given appropriate training on due diligence principles and procedures that they can then utilise in investigating their supply chains and knowing what to do with what they learn.
Company and Supplier Willingness
A company is comprised of professionals from different educational, disciplinary, political and socioeconomic backgrounds. While every member of a team is invested in driving success in the business, some may consider responsible sourcing low on the priority list. Internal and external resistance can stall a company’s progress towards responsible sourcing, and must be identified and addressed.
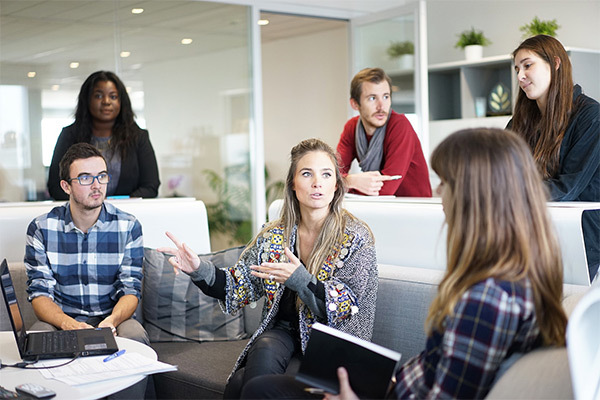
Internal resistance can come from shareholders, management and employees that are not aware of the benefits of responsible sourcing, the risks of not doing it, and the severity of the potential risks. In larger companies, it’s often especially difficult to communicate the need for transparency and risk controls up or down the hierarchy.
External resistance can come from suppliers that do not take their obligation to provide detailed information on their supply chains seriously. In the jewellery and raw materials sourcing industries there can be a culture of close, and often closed, supplier relationships, making it tough to demand change. We’ll unpack that concept further in next week’s blog.
Resistance to change can stall the dialogue processes integral to companies developing a better business approach. This is why it often takes reports like ‘The Hidden Cost of Jewelry’ to raise consumer and investor awareness and promote dialogue on sourcing practices across precious metal and mineral supply chains.
So, how should you start to build capacity? Jewellery companies, large and small, can do the following:
- Join and utilise the services of relevant industry associations. Ask them to provide you with capacity building and guidance services that are broad in scope. This should cover not only due diligence on supply chains, but what human and environmental risks mean in practice, what your company can do to manage those risks, and how the industry association helps tackle these risks at sector level. Ask your associations to offer guidance when you face difficult decisions. This will increase your resource and knowledge capacity.
- Get buy-in from your whole company. This should be led by senior management and communicated to employees. Once you’ve got your team on board, you can delegate responsibility for various due diligence tasks to speed up the implementation of your action plan.
- Anybody involved in your sales function also needs to be in the loop regarding how the company is now managing supply chain risks, both as a value-add and to respond to customer queries.
- Expand your own knowledge base. There are a number of tools and recommended readings, some of which are business or company size-specific, to kick off this process – we’ve listed some of them below.
- Communicate your due diligence intentions to your suppliers well in advance. Let them know what you will require from them, and by when. Make sure they know this is important to your ongoing working relationship. Don’t assume they’ll be ready to comply - they may need to be sold on the concept, too. Increasing pressure on companies to develop responsible supply chains means that your suppliers will likely receive similar requests from other buyers. Be sure to communicate the importance of them getting started now in order to develop a competitive advantage.
So far in our Better Business blog series, we’ve explored the benefits and opportunities provided by transparent supply chains and traceable materials, and we’ve addressed some common capacity barriers. Next week, Responsible Sourcing and Development Specialist Victoria Gronwald considers how culture can limit companies’ willingness and ability to embrace a better business approach.
Recommended reading:
OECD Due Diligence Guidance for Responsible Business Conduct
Study on the Support System for SME Supply Chain Due Diligence (Project report for an SME-focused supply chain due diligence briefing document that will be published by the European Commission in the future)
Ethical Corporation: '60% of companies are integrating the SDGs into business strategy'
Responsible Jewellery Council: Responsible Sourcing of Coloured Gemstones
The 'Better Business in the Jewellery Sector' blog series is written by jewellery, due diligence, and responsible sourcing experts from Levin Sources and edited by Dr. Yolande Kyngdon-McKay and Jack Cooper. Estelle Levin-Nally provides editorial oversight, analysis and additional contributions.